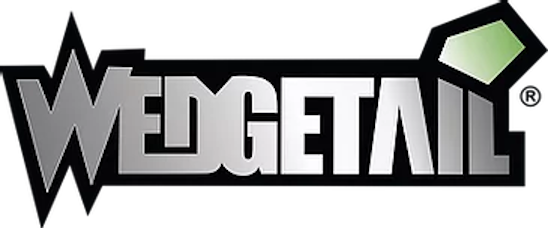

PRODUCT
INFORMATION
WEDGETAIL PLATFORM ROOF RACK – PRODUCT INFORMATION
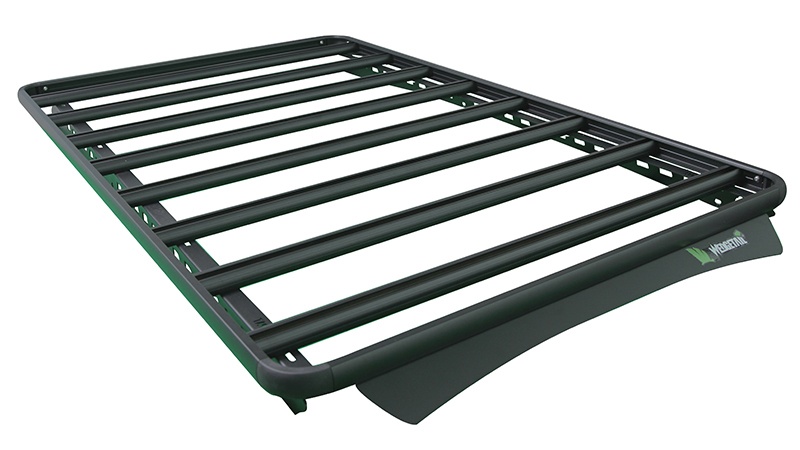
The Wedgetail platform roof rack has been developed to fill the need for a new generation composite assembly platform roof rack with the strength to maintain its full load rating on the toughest of off-road tracks.
Built to fit a wide range of 4x4 utes and wagons and selected vans, the Wedgetail platform roof rack is fitted onto a set of mounting rails that are bolted to mounting lugs connected into the sub-structure of the roof or onto the roof gutters and held in place by bolt-on clips.
These mounts spread the weight of the roof rack and its load over the whole mounting system and have the strength to cope with extended periods of off-road use.
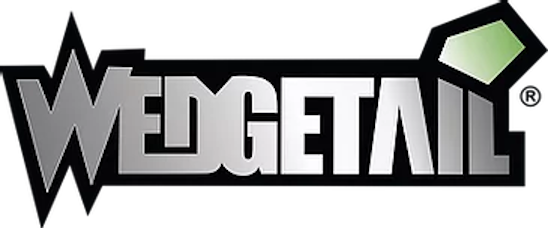
WEDGETAIL PLATFORM
ROOF RACK
– PRODUCT INFORMATION
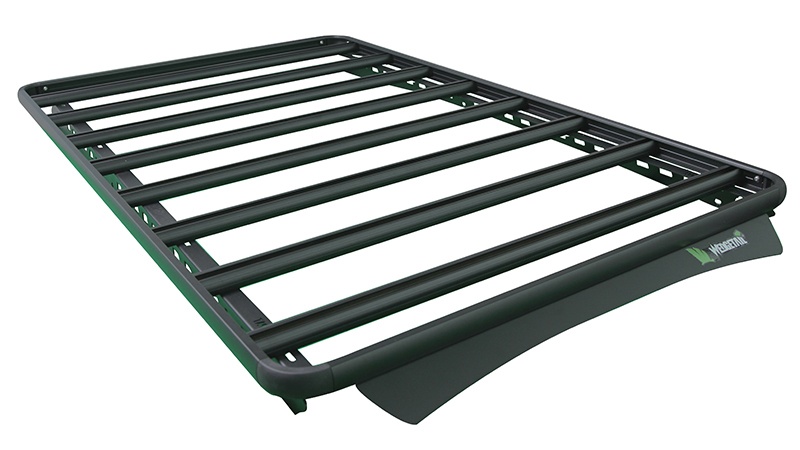
The Wedgetail platform roof rack has been developed to fill the need for a new generation composite assembly platform roof rack with the strength to maintain its full load rating on the toughest of off-road tracks.
Built to fit a wide range of 4x4 utes and wagons and selected vans, the Wedgetail platform roof rack is fitted onto a set of mounting rails that are bolted to mounting lugs connected into the sub-structure of the roof or onto the roof gutters and held in place by bolt-on clips.
These mounts spread the weight of the roof rack and its load over the whole mounting system and have the strength to cope with extended periods of off-road use.
DEVELOPMENT AND TESTING
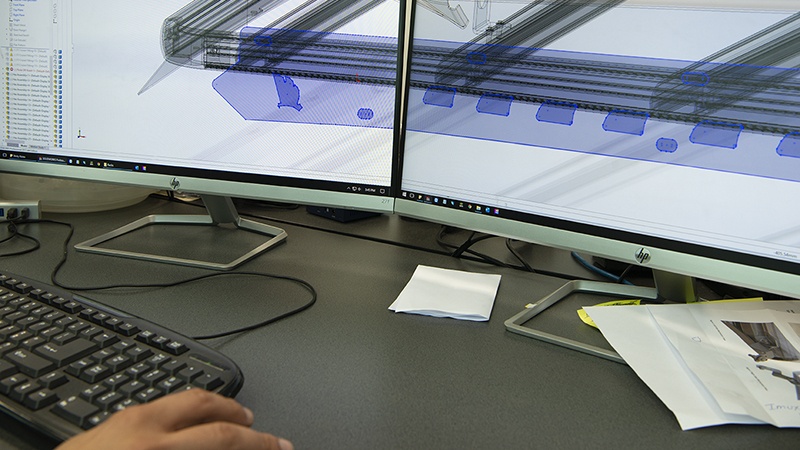
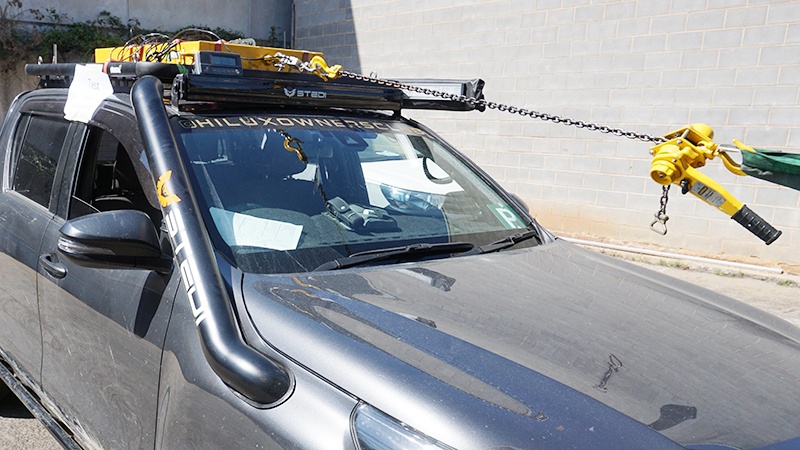
Design
The Wedgetail rack was developed by our team of engineers to take advantage of custom designed components and new composite materials. Super strong aluminium was moulded into two profiles for use in the platform frame and for the crossbars. A number of materials were tested for use as the corner fittings until the final components were approved.
Testing
A series of prototypes were manufactured and stress tested on a range of vehicles and on the toughest offroad tracks with the maximum load allowed. The Wedgetail rack went through two years of development and testing before it was approved for manufacture.
COMPONENTS
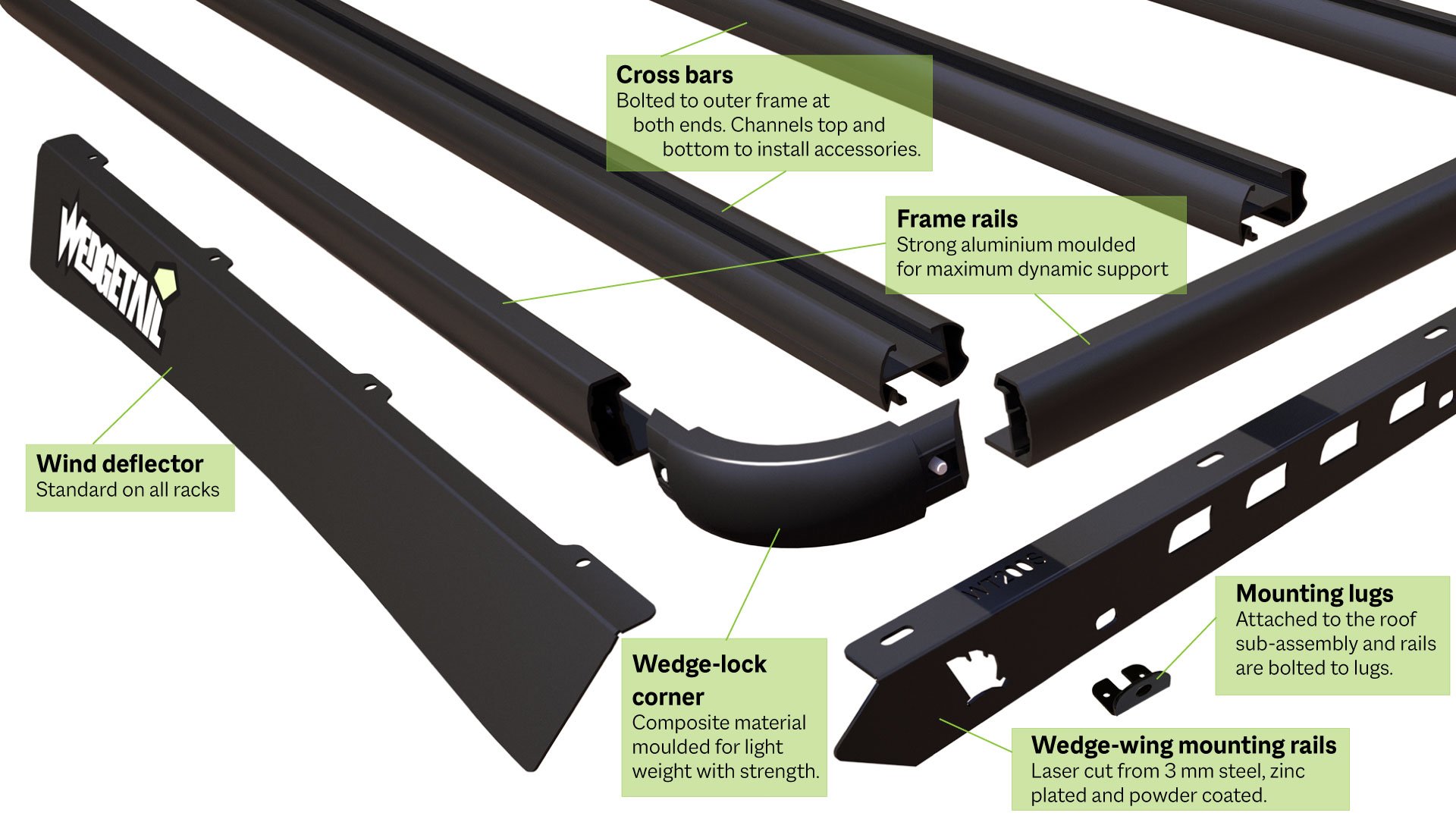
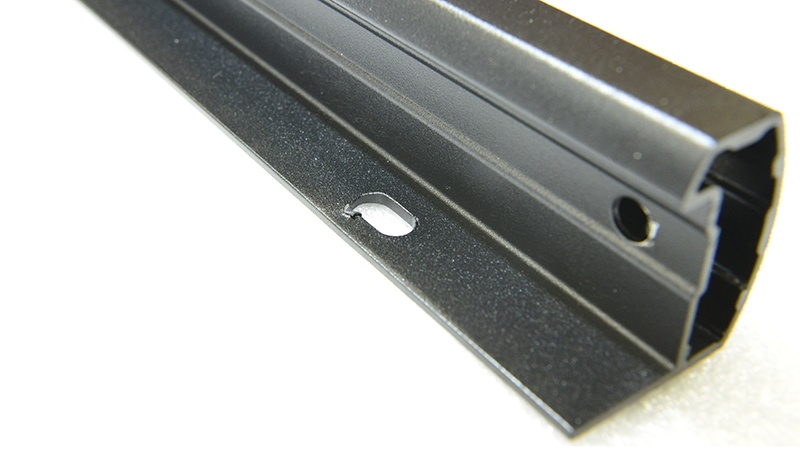
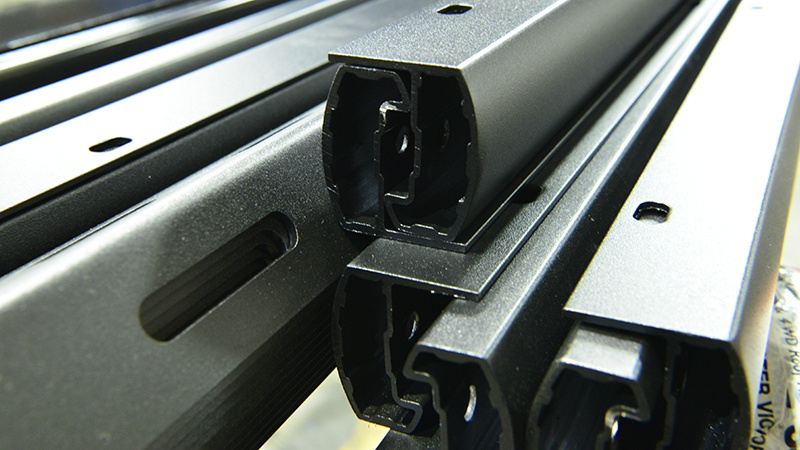
Frame and crossbars
Manufactured using 6060 grade aluminium and extruded in Australia to custom profiles for use as frame components or as crossbars. The frame components are designed for maximum dynamic strength while the crossbars are designed to withstand the direct downwards pressures generated by the weight of items carried on the rack or by accessories fitted on the crossbars.
The frame bars are pre-punched with holes at between 250 and 310 mm spacing for locating of crossbars and fixing of wind deflectors.
All bar components are powder coated in matt black.
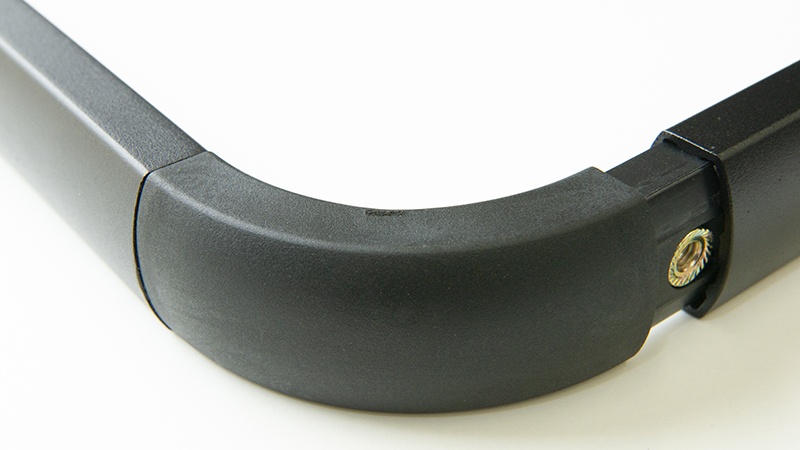
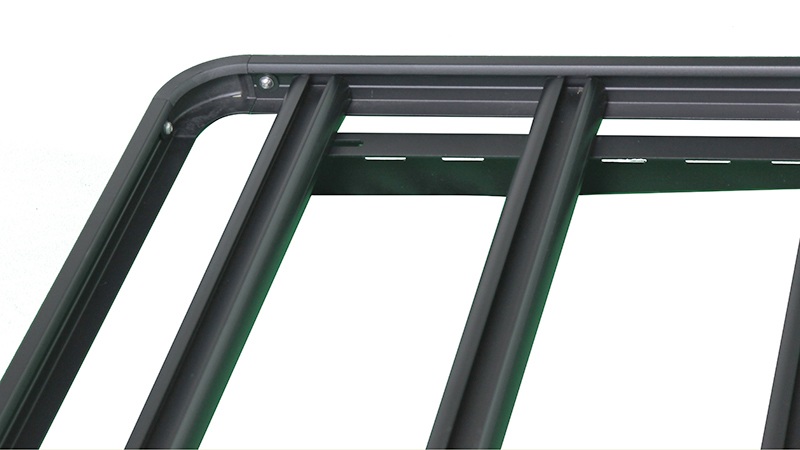
Wedge-lock corner units
The corner units are moulded using a composite of nylon and glass-reinforcing mixed with other strengthening substances. Once cast the corner units are machined to remove surplus materials and mounting holes are drilled.
The Wedge-lock corner units have a flanged nut inserted into the outside of the bolt hole. The ends of the corner units are fitted into the frame rails and 8 mm stainless steel bolts are used to fix them in place, creating a strong joint.
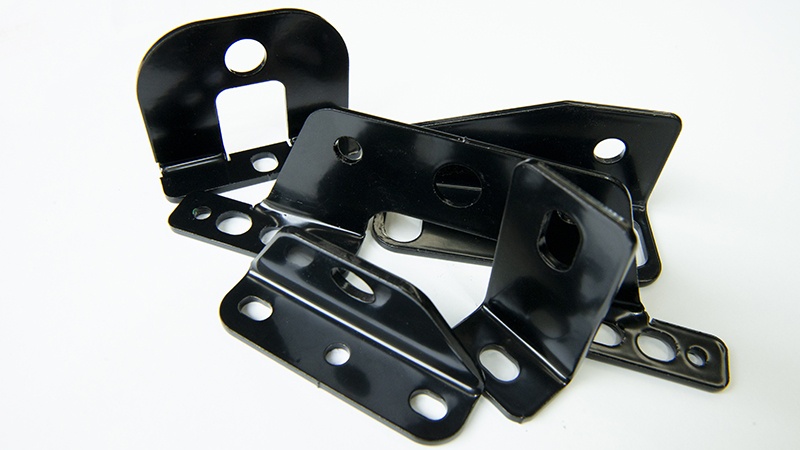
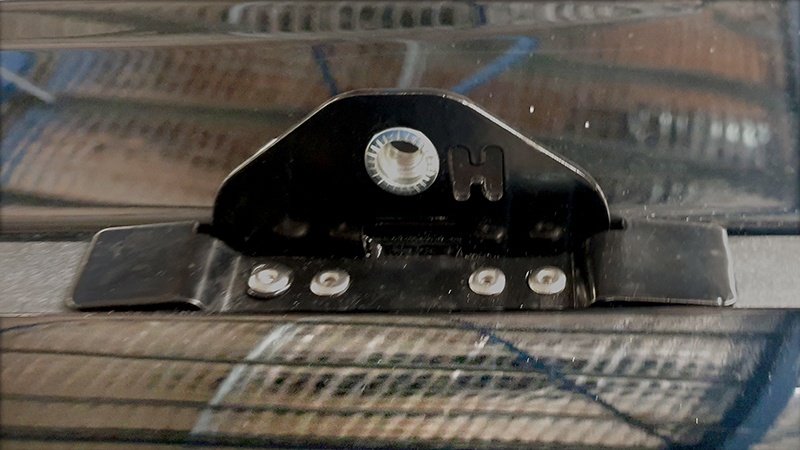
Mounting lugs
The mounting lugs are used to attach to mounting points built into the sub-structure of the vehicle roof. Once the fixing lugs are installed the mounting rails are bolted to the lugs. The lugs are designed for individual models of vehicle and a variety of fixing devices are used for the lugs. Most vehicles with factory fitted rails will have bolt in points so they are used.
If bolt in points are not available we will drill through to the sub-structure of the roof and use stainless steel rivets to fix the tabs. All holes are then water proofed using a commercial grade silicon sealant.
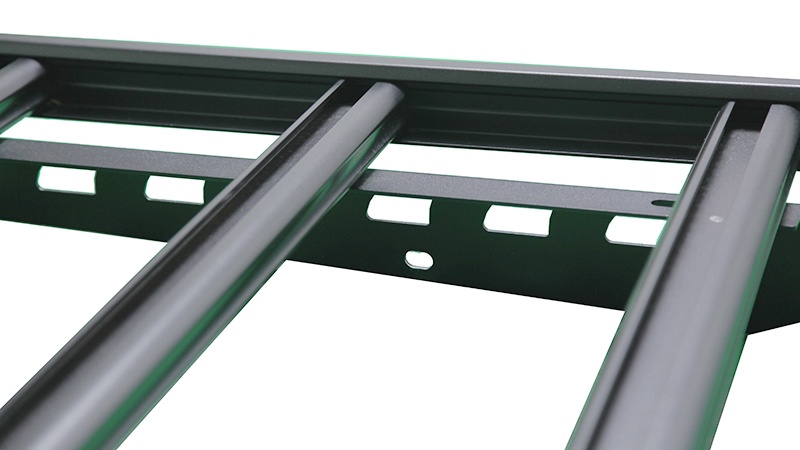
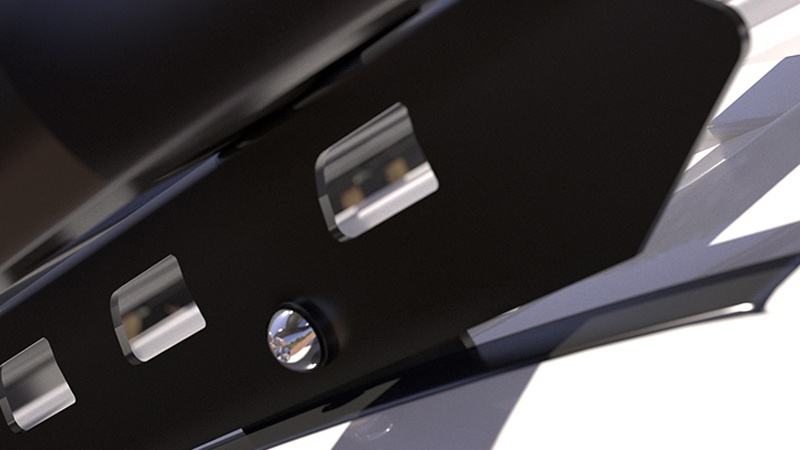
Wedge-wing mounting rails
The mounting rails are custom designed for each vehicle so that the weight of the platform and load is evenly spread over the vehicle roof. The mounting rails are laser cut from 3 mm steel and then zinc electro-plated and powder coated with a matt black finish.
The mounting rails for all utes and wagons are a single piece and for vans each side is made up of two sections.
The mounting rails and lugs and all bolts required are packed into cartons for shipping.
ASSEMBLY
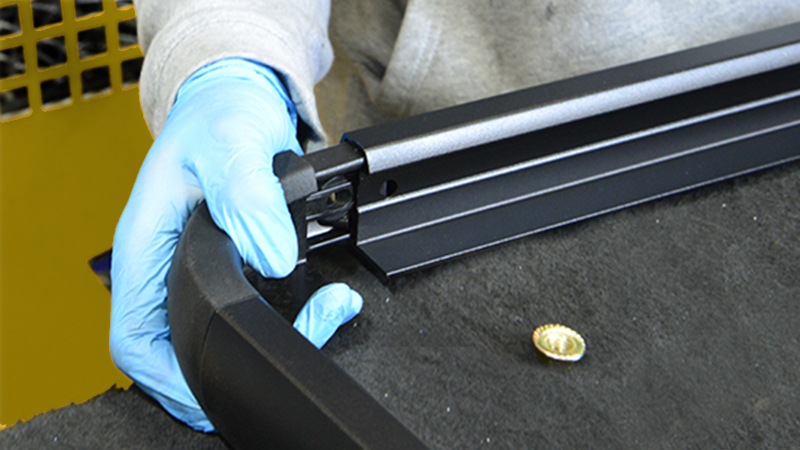
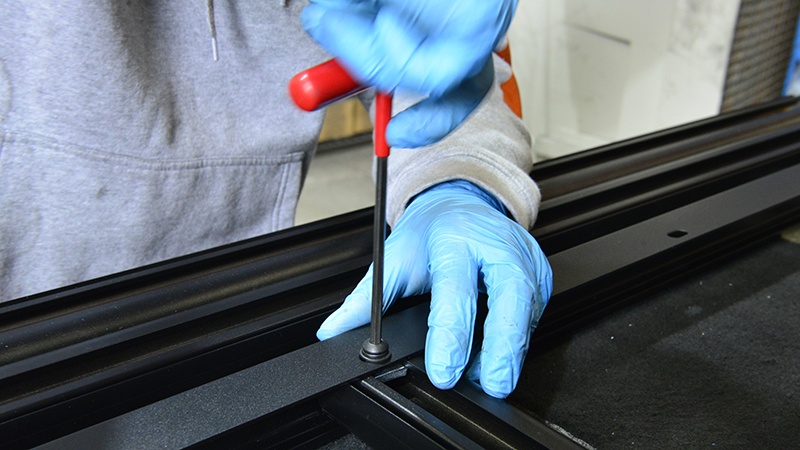
All platforms are assembled in our manufacturing centre in Bayswater Victoria. All components are cut to the required length and holes are punched in the platform frame rails at even spacing (between 250 and 310 mm).
The platform frame is built first and then the crossbars are added. The crossbars are bolted to the bottom flange of the frame rails using 8 mm stainless steel bolts. The corner units are then tightened and checked to ensure the frame is square and then all bolts are tightened to the specified torque.
The platforms are manufactured in a range of sizes to suit 4 wheel drive ute's and wagons and a number of vans.
The platform is then wrapped in plastic and packaged in a strong cardboard carton and labelled ready for shipment.
Custom builds
We can custom build a roof rack to allow breaks in the crossbars for vents or skylights. This is applicable mainly to vans. Any custom build needs to be specified fully with complete dimensions. Custom builds must be ordered directly or through a reseller.
PACKING AND FREIGHT
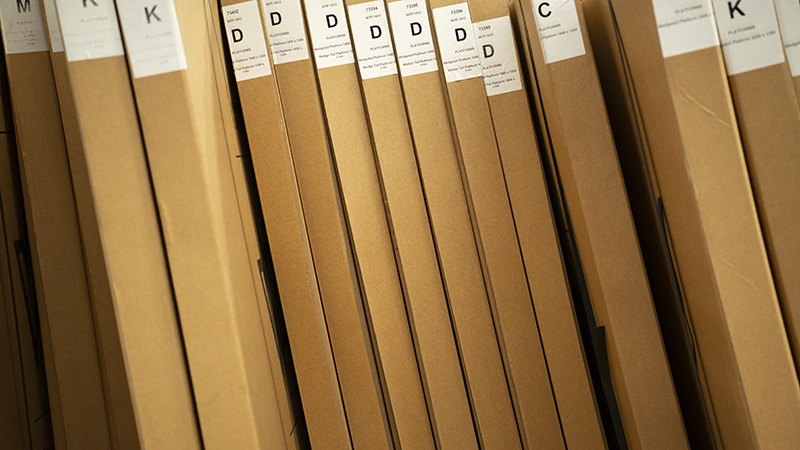
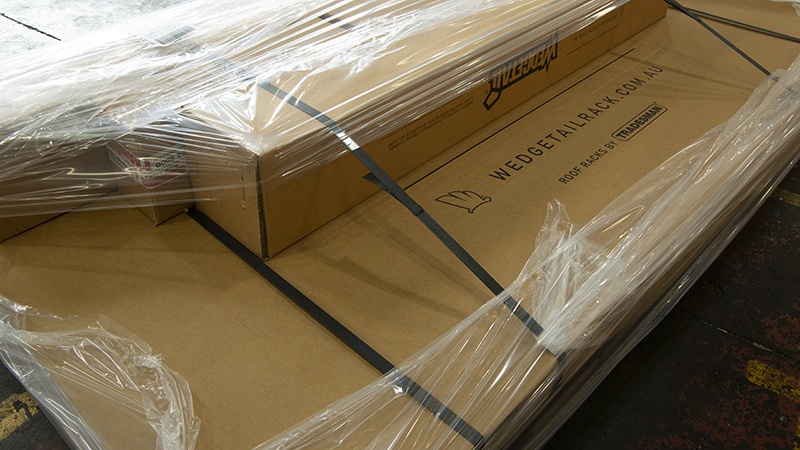
Platforms are plastic wrapped and packed in a cardboard carton. The mounting rails, wind deflector, mounting lugs, all bolts or rivets required and a set of installation instructions are packaged into a second carton. The cartons are then placed on a shipping pallet, polyester strapping added and plastic wrapping applied to protect the shipment.
Wedgetail racks are dispatched by road freight to locations throughout Australia.
Vehicle specific installation instructions are included with all racks.
DEVELOPMENT AND TESTING
Design
The Wedgetail rack was developed by our team of engineers to take advantage of custom designed components and new composite materials. Super strong aluminium was moulded into two profiles for use in the platform outer frame and for the crossbars. A number of materials were tested for use as the corner fittings until the final components were approved.
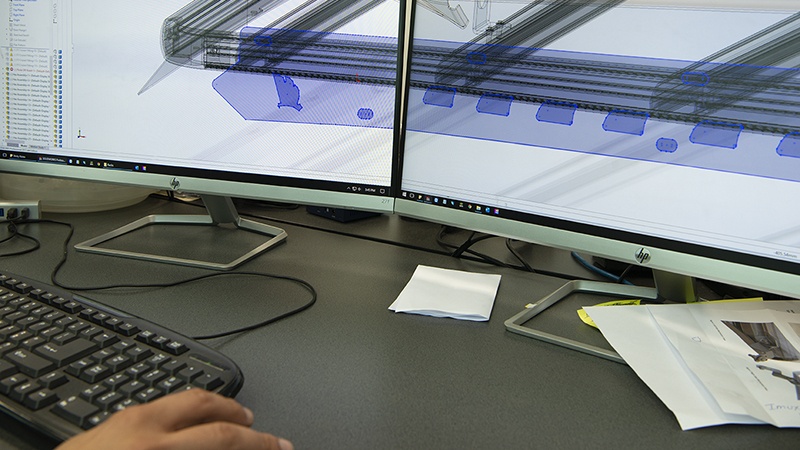
Testing
A series of prototypes were manufactured and stress tested on a range of vehicles and on the toughest offroad tracks with the maximum load allowed. The Wedgetail rack went through two years of development and testing before it was approved for manufacture.
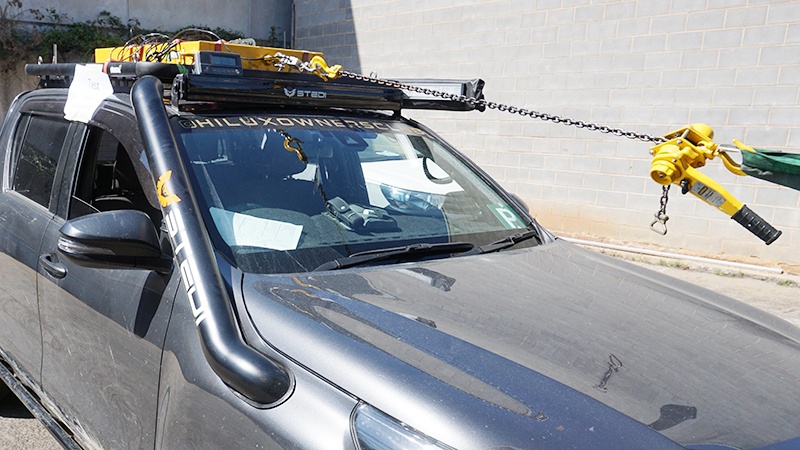
COMPONENTS
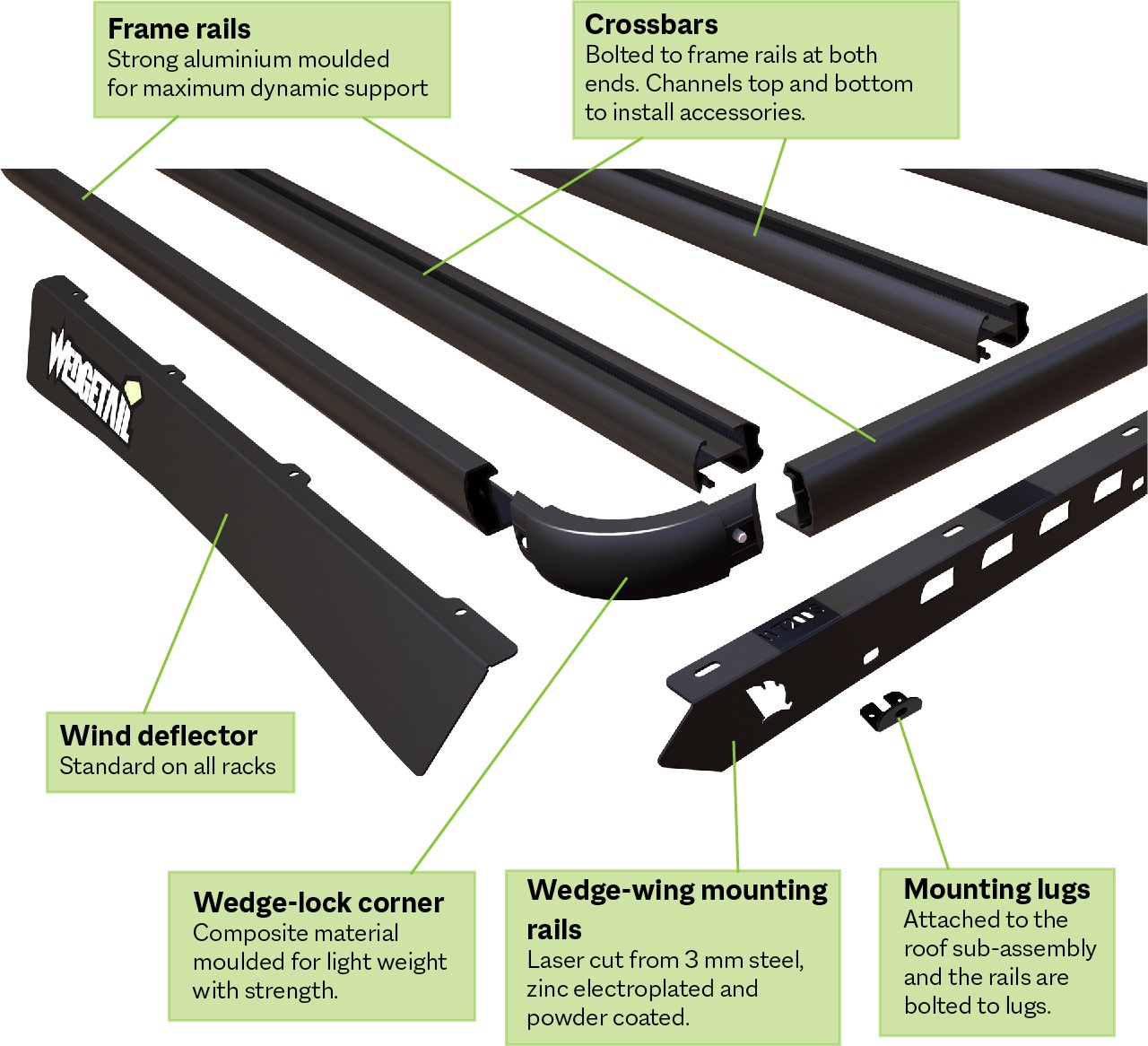
Frame and crossbars
Manufactured using 6060 grade aluminium and extruded in Australia to custom profiles for use as frame components or as crossbars. The frame components are designed for maximum dynamic strength while the crossbars are designed to withstand the direct downwards pressures generated by the weight of items carried on the rack or by accessories fitted on the crossbars.
The frame bars are pre-punched with holes at between 250 and 310 mm spacing for locating of crossbars and fixing of wind deflectors.
All bar components are powder coated in matt black.
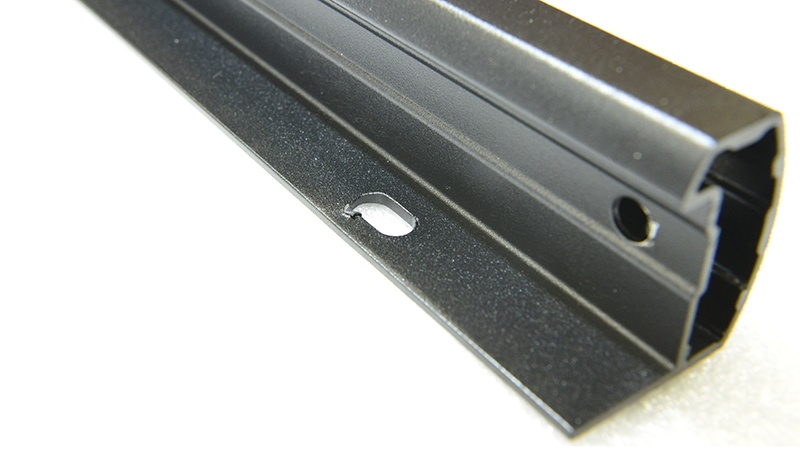
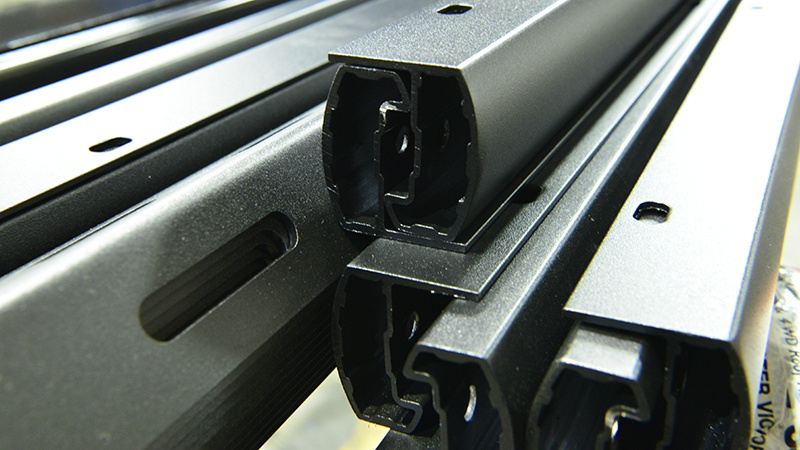
Wedge-lock corner units
The corner units are moulded using a composite of nylon and glass-reinforcing mixed with other strengthening substances. Once cast the corner units are machined to remove surplus materials and mounting holes are drilled.
The Wedge-lock corner units have a flanged nut inserted into the outside of the bolt hole. The ends of the corner units are fitted into the frame rails and 8 mm stainless steel bolts are used to fix them in place, creating a strong joint.
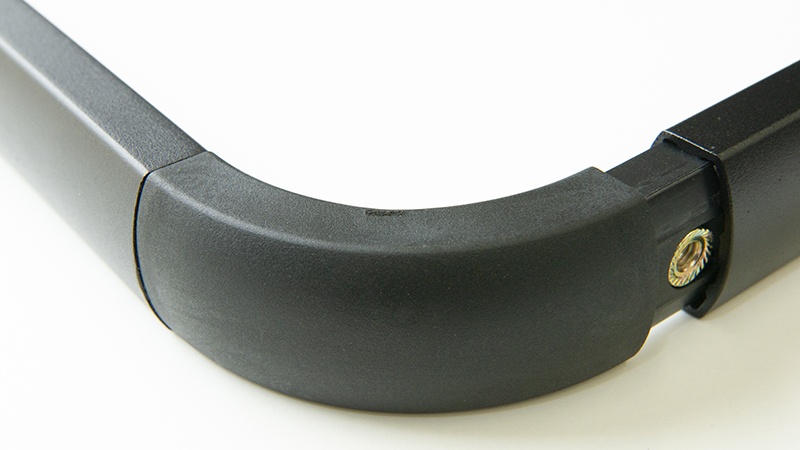
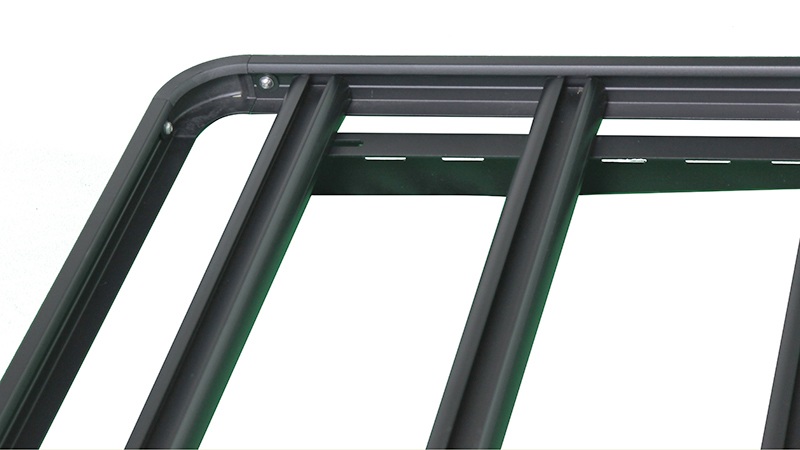
Mounting lugs
The mounting lugs are used to attach to mounting points built into the sub-structure of the vehicle roof. Once the fixing lugs are installed the mounting rails are bolted to the lugs. The lugs are designed for individual models of vehicle and a variety of fixing devices are used for the lugs. Most vehicles with factory fitted rails will have bolt in points so they are used.
If bolt in points are not available we will drill through to the sub-structure of the roof and use stainless steel rivets to fix the lugs. All holes are then water proofed using a commercial grade silicon sealant.
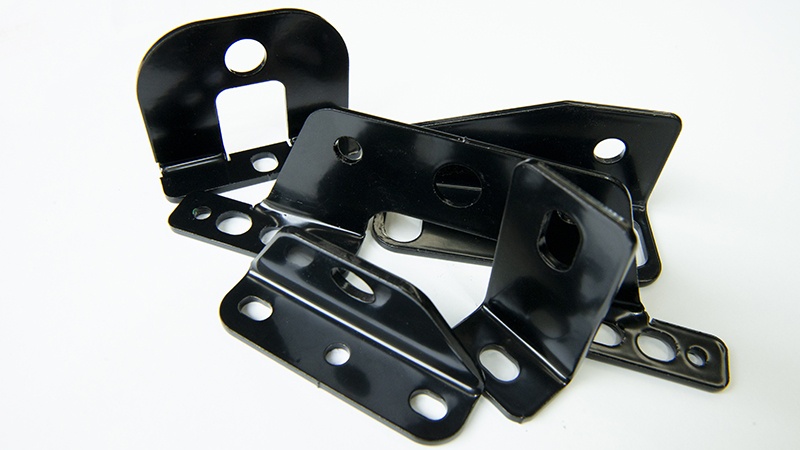
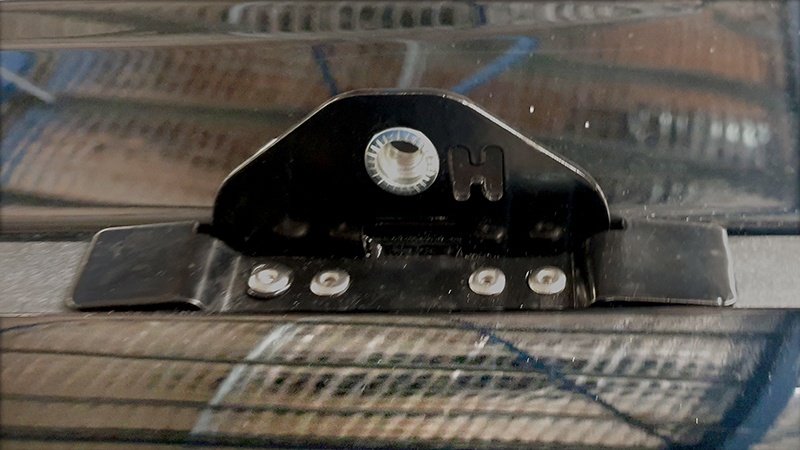
Wedge-wing mounting rails
The mounting rails are custom designed for each vehicle so that the weight of the platform and load is evenly spread over the vehicle roof. The mounting rails are laser cut from 3 mm steel and then zinc electro-plated and powder coated with a matt black finish.
The mounting rails for all utes and wagons are a single piece and for vans each side is made up of two sections.
The mounting rails and fixing tabs and all bolts required are packed into cartons for shipping.
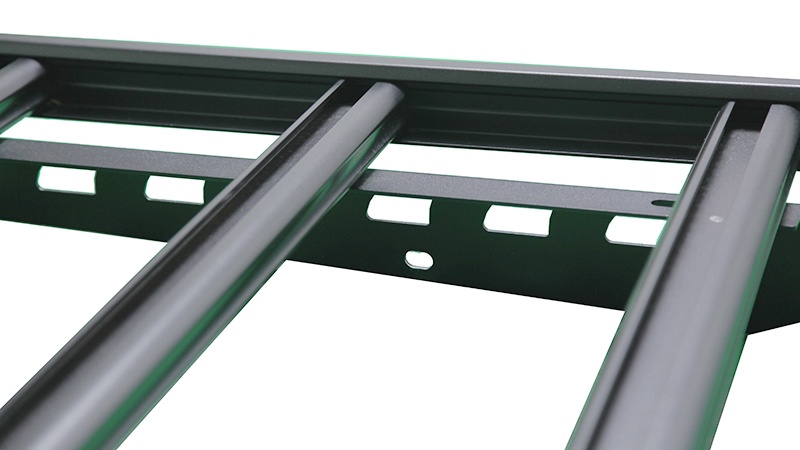
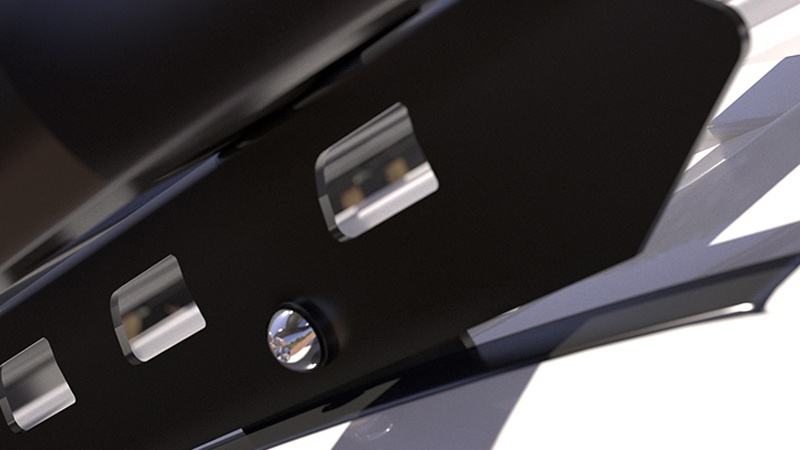
ASSEMBLY
All platforms are assembled in our manufacturing centre in Bayswater Victoria. All components are cut to the required length and holes are punched in the platform frame rails at even spacing (between 250 and 310 mm).
The platform frame is built first and then the crossbars are added. The crossbars are bolted to the bottom flange of the frame rails using 8 mm stainless steel bolts. The corner units are then tightened and checked to ensure the frame is square and then all bolts are tightened to the specified torque.
The platforms are manufactured in a range of sizes to suit 4 wheel drive ute's and wagons and a number of vans.
The platform is then wrapped in plastic and packaged in a strong cardboard carton and labelled ready for shipment.
Custom builds
We can custom build a roof rack to allow breaks in the crossbars for vents or skylights. This is applicable mainly to vans. Any custom build needs to be specified fully with complete dimensions. Custom builds must be ordered directly or through a reseller.
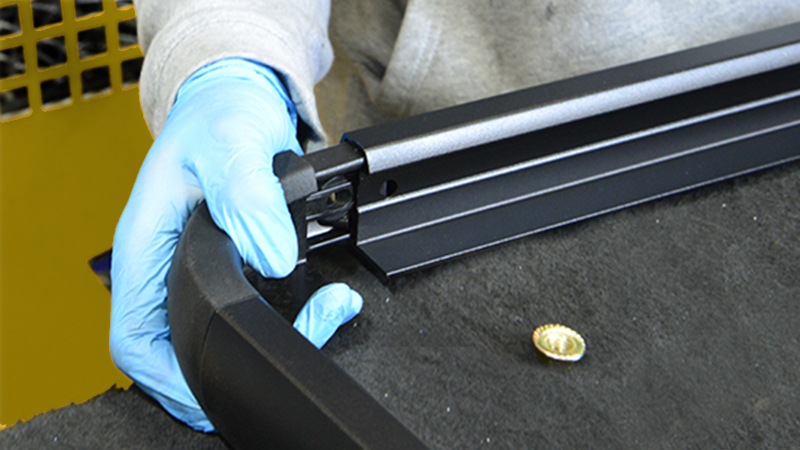
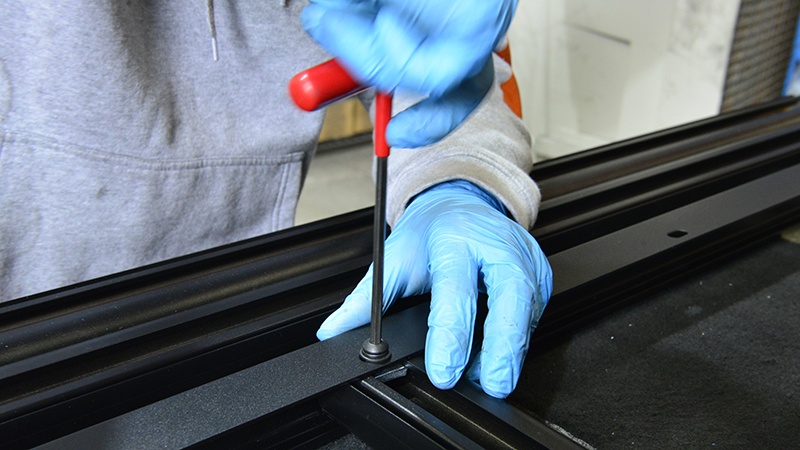
PACKING AND FREIGHT
Platforms are plastic wrapped and packed in a cardboard carton. The mounting rails, wind deflector, mounting lugs, all bolts or rivets required and a set of installation instructions are packaged into a second carton. The cartons are then placed on a shipping pallet, polyester strapping added and plastic wrapping applied to protect the shipment.
Wedgetail racks are dispatched by road freight to locations throughout Australia.
Vehicle specific installation instructions are included with all racks.
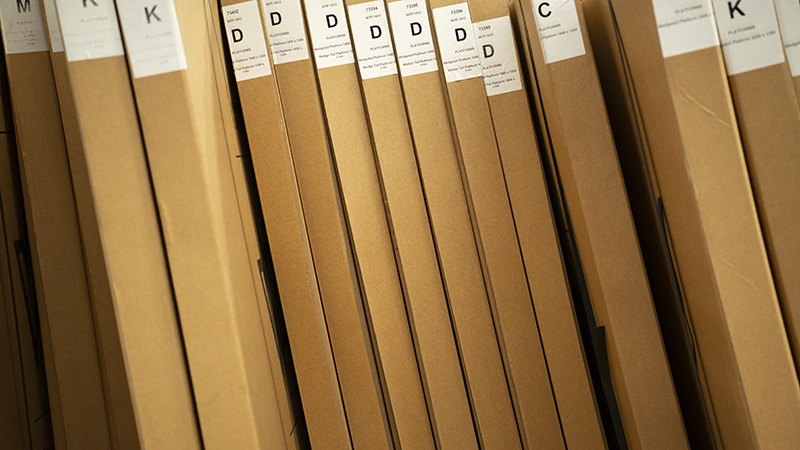
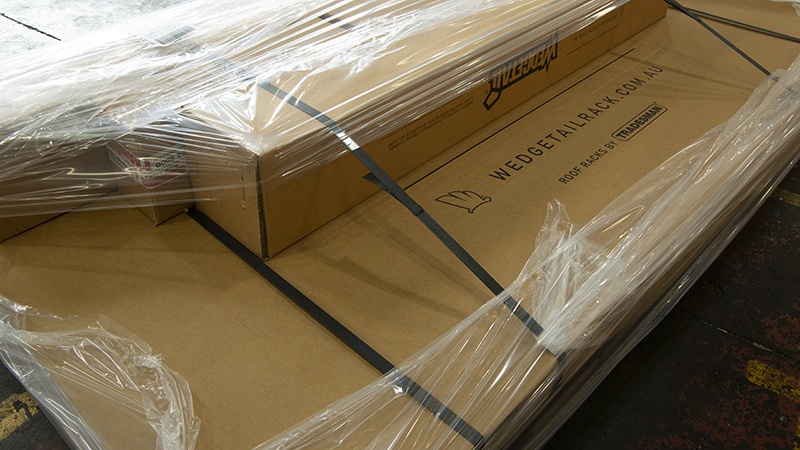